Operation method and precautions of flat die D-type pellet mill
Requirements for raw materials
- Pellet mill for different raw materials have different moisture requirements, wood D-type pellet mill ZLSP-D usually requires raw material moisture of 10%-18%, and well mixed.
- The maximum size of raw materials required for pelleting shall not exceed the diameter of die hole.
- You can use a single raw material, different raw materials can also be mixed, but raw materials may not be mixed with iron, stones and other hard objects, otherwise it will damage the machine.
- Using our company's products without any additives, we can achieve high quality pelletizing effect. But in order to increase output and extend service life of dies and rollers, it is recommended to use adhesives reasonably.
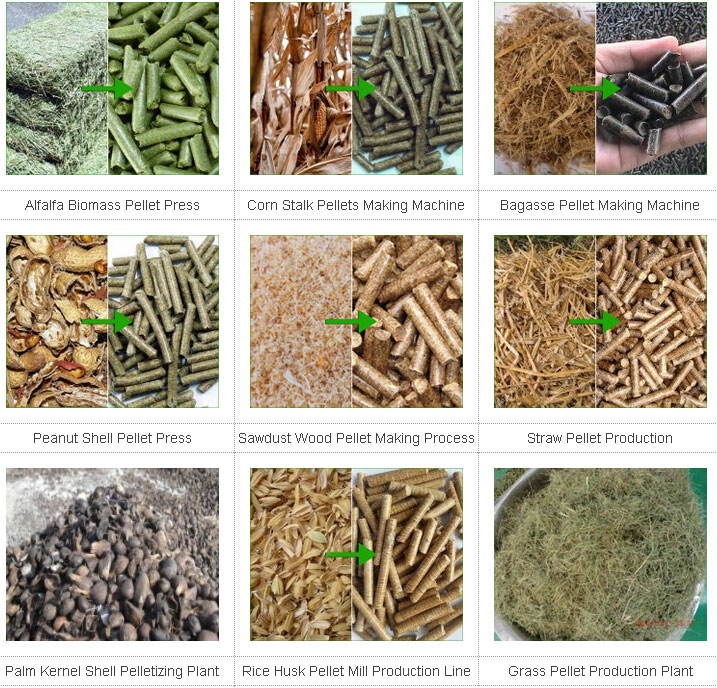
The grinding-in and adjusting of flat die D-type pellet mill
New flat die grinding-in
Flat die should be ground before the first use, the method is as follows. Take 5 kg of raw materials, 1 kg of fine sand stir, then add 1 kg of waste oil and mix thoroughly. Start the machine, put the ingredients into a feeder, wrench adjusts roller bolts until the normal discharge so far. (Note: the adjustment gap can not be too small, too small will damage the roller and flat die.) Keep the machine running for 1 hour and then add the normal raw materials for production. If you can not a normal granulation, the roller bolt should be slightly loosed to normal.
After adjustment still can not normally out of pellets, you can use nail to reveal the oil or drier in the flat die, and then re-run.
When the operator to complete the day's granulation work and the pressing of the raw material in the granulation room, filling the die hole with oil material to ensure that the die hole is not blocked. This operator will be ready for the next operation, the next time you start the device will save a lot of time.
Adjustment of roller and flat die gap
The gap between the roller and the flat die has a great influence on the quality of granulating, and the general gap should be between 0.05 mm and 0.3 mm. When the gap is greater than 0.3 mm, the material layer is too thick and unevenly distributed, reducing the production of granulation. When the gap is less than 0.05 mm, the wear of the machine is serious. Method of judging the distance between roller and die:
Die hole depth and aperture (compression ratio) of the choice
The compression ratio is the ratio of die hole depth and aperture. The compression ratio is small, the production of granulating is high, but the hardness is low. On the contrary, the yield is low and the hardness is high. Therefore, the user should choose different flat die according to the needs, if necessary, can provide raw materials, we customize the die plate for your needs.
Adjustment of pellet length
Adjust the length of the pellet by adjusting the height of the knife provided on the edge of the discharge opening.
Replacement method of flat die
Using a screwdriver to flatten the spindle washer into one of the notched teeth of the nut, unscrewing the nut with a hook wrench (spare part), removing the washer and flat washer, and removing the die plate with a die plate driver (spare part). After replacing the new flat die, according to the above method to re-run.
Processed pellet treatment
Processed pellets temperature is relatively higher, which should be placed in a ventilated place, cooled to room temperature before bagging storage.